POSITION: SQE&SDE SupervisorDEPARTMENT/Function: Supply Chain ManagementREPORTS TO: Supply Chain Manager POSITION SUMMARYThe primary function of the Supplier Quality & Supplier Development (SQE&SDE) Supervisor is to lead SQE & SDE team on supplier development initiatives, including supplier performance management, supplier certification, supplier quality issue data collection and analysis, supplier compliance with company requirements, supplier forums, newsupplier quality assessment, supplier APQP development and tracking, and supplier quality continuous improvement.
ACCOUNTABILITIESPotential supplier assessment and development
a. Work with Purchasing, Engineering and Quality, evaluate and qualify potential suppliersb. Do potential supplier audit per ISO/TS 16949;
c. Define a corrective action plan tracking list to develop suppliers to meet BW requirement;
Support new project launch
a. Follow up supplier APQP development and tracking
b. Clear understand requirements on the drawing, in particular all key product characteristics (KPC);
c. Clear understand the key characteristics control in supplier process with control methods;
d. Sample submitting with related document such as material, functional and dimension check report;
e. Supplier PPAP document developing per PPAP manual including engineering change requirements;
f. Supplier PPAP review and on side audit to consistency;
g. Supplier PPAP approval (final approval shall be done by Quality manager);
Supplier quality managementa. Be responsible for CPM management;b. Initial follow-up on supplier containment and corrective action.c. Be responsible for supplier 8D review of actions and supporting documentation, validation and closure. d. Issuance, Follow-up, & Removal of suppliers from Controlled Shipping Levels 1 & 2 if required.e. Organize Quarterly Worst Supplier Reviews & Supplier Improvement programs Supplier performance maintenance
a. Approved supplier list maintenance;
b. Make quality performance report monthly such as PPM, incident number and defects analysis;
c. Maintain supplier quality performance in BW Supplier Performance System (SPS);d. Make sure all suppliers access to SPS to review their score card at least once a month;
e. Engineering change follow-up including subcontract, material & tooling and process etc.;
f. Conduct annual supplier process audit.
Continuous improvement
a. Push suppliers to make action plans to improve their performance (quality, delivery and response) based on their score card, and follow up their action plansb. Coach and/or mentor suppliers on performance improvement.
c. Train suppliers in APQP, PPAP, MSA, SPC, FMEA etc.
Other assigned joba. Support cost reduction, quality improvement, cycle time reduction and flexibility improvement programs.b. Support Global SDE team's activitiesc. Direct and oversee the work of team specialists.
d. Develop team budget and manage team expenses.
REQUIREMENTSDegree Requirements: Bachelor's degree in Engineering or Manufacturing is required
Other Qualifications: 10 years work experience in manufacturing/quality (Preferred on Casting, Machining, Powder Metal, Stamping, Forging, Rub & Plastics) 3-5 years of Supplier Development & Quality Engineering experience in the automotive industry; At least 2 years SDE/SQE team leader/supervisor experience Knowledge in manufacturing problem solving (8-D Methodology) and manufacturing processes required; Knowledge of TS16949 requirements including AIAG APQP, PFMEA, MSA, SPC and PPAP required; Proven leadership abilities; Effective at defining problems, collecting data, establishing facts and drawing valid conclusions. Ability to interpret a variety of technical instructions in mathematical or diagram form and deal with abstract and/or concrete variables. Proficient in general business correspondence to external suppliers. Effective communication skills to clearly articulate supplier defect issues and to respond to questions regarding these issues; Good English in writing and speak;Proficient in Microsoft Word, Excel & Outlook.
TEN COMPETENCIES Priority Setting Decision Quality Problem Solving Process Management Functional/Technical Skills Interpersonal Savvy Action Oriented Timely Decision Making Drive for Results Informing
ACCOUNTABILITIESPotential supplier assessment and development
a. Work with Purchasing, Engineering and Quality, evaluate and qualify potential suppliersb. Do potential supplier audit per ISO/TS 16949;
c. Define a corrective action plan tracking list to develop suppliers to meet BW requirement;
Support new project launch
a. Follow up supplier APQP development and tracking
b. Clear understand requirements on the drawing, in particular all key product characteristics (KPC);
c. Clear understand the key characteristics control in supplier process with control methods;
d. Sample submitting with related document such as material, functional and dimension check report;
e. Supplier PPAP document developing per PPAP manual including engineering change requirements;
f. Supplier PPAP review and on side audit to consistency;
g. Supplier PPAP approval (final approval shall be done by Quality manager);
Supplier quality managementa. Be responsible for CPM management;b. Initial follow-up on supplier containment and corrective action.c. Be responsible for supplier 8D review of actions and supporting documentation, validation and closure. d. Issuance, Follow-up, & Removal of suppliers from Controlled Shipping Levels 1 & 2 if required.e. Organize Quarterly Worst Supplier Reviews & Supplier Improvement programs Supplier performance maintenance
a. Approved supplier list maintenance;
b. Make quality performance report monthly such as PPM, incident number and defects analysis;
c. Maintain supplier quality performance in BW Supplier Performance System (SPS);d. Make sure all suppliers access to SPS to review their score card at least once a month;
e. Engineering change follow-up including subcontract, material & tooling and process etc.;
f. Conduct annual supplier process audit.
Continuous improvement
a. Push suppliers to make action plans to improve their performance (quality, delivery and response) based on their score card, and follow up their action plansb. Coach and/or mentor suppliers on performance improvement.
c. Train suppliers in APQP, PPAP, MSA, SPC, FMEA etc.
Other assigned joba. Support cost reduction, quality improvement, cycle time reduction and flexibility improvement programs.b. Support Global SDE team's activitiesc. Direct and oversee the work of team specialists.
d. Develop team budget and manage team expenses.
REQUIREMENTSDegree Requirements: Bachelor's degree in Engineering or Manufacturing is required
Other Qualifications: 10 years work experience in manufacturing/quality (Preferred on Casting, Machining, Powder Metal, Stamping, Forging, Rub & Plastics) 3-5 years of Supplier Development & Quality Engineering experience in the automotive industry; At least 2 years SDE/SQE team leader/supervisor experience Knowledge in manufacturing problem solving (8-D Methodology) and manufacturing processes required; Knowledge of TS16949 requirements including AIAG APQP, PFMEA, MSA, SPC and PPAP required; Proven leadership abilities; Effective at defining problems, collecting data, establishing facts and drawing valid conclusions. Ability to interpret a variety of technical instructions in mathematical or diagram form and deal with abstract and/or concrete variables. Proficient in general business correspondence to external suppliers. Effective communication skills to clearly articulate supplier defect issues and to respond to questions regarding these issues; Good English in writing and speak;Proficient in Microsoft Word, Excel & Outlook.
TEN COMPETENCIES Priority Setting Decision Quality Problem Solving Process Management Functional/Technical Skills Interpersonal Savvy Action Oriented Timely Decision Making Drive for Results Informing
職位類別: 生產經理/車間主任
舉報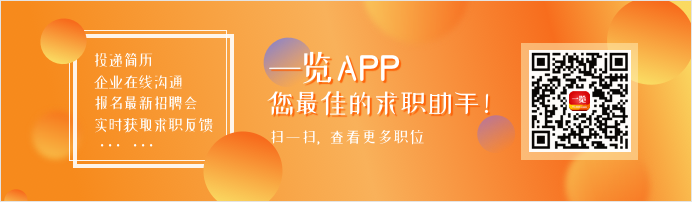
- 公司規(guī)模:500 - 999人
- 公司性質:外商獨資
- 所屬行業(yè):零部件
- 所在地區(qū):浙江-寧波市
- 聯系人:Human Resource
- 手機:會員登錄后才可查看
- 郵箱:會員登錄后才可查看
- 郵政編碼:315000
工作地址
- 地址:寧波市鄞州區(qū)金谷中路188號